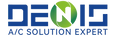
Core Advantages
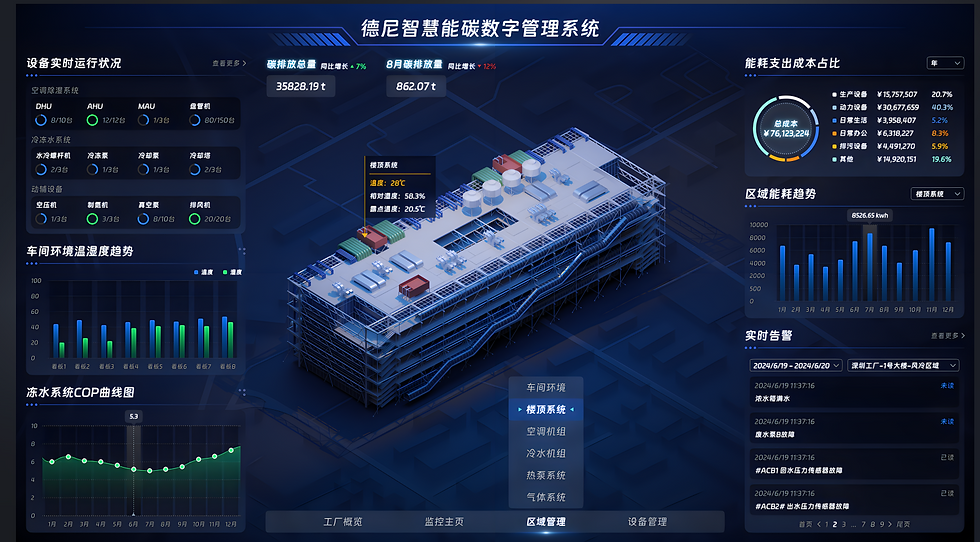
New energy low humidity clean room and energy saving air conditioning system
Lithium battery production environment almost the whole process in a low-humidity environment, humidity requirements are generally required below 1% RH, even as low as 0.1% RH, the production environment is large, the number of people is small, the conventional design will lead to dehumidification equipment initial investment is high as well as air-conditioning operating costs are also extremely high. After years of design experience, Denis's has developed a system solution for temperature, humidity and cleanliness separation control, and has applied for a patent.
Eg. A lithium-ion plant bidding drawings design program used the traditional design, resulting in dehumidification equipment air volume, high initial investment and high operating costs. Denis environment proposed energy-saving patent program for customers to save investment costs of 10 million (dehumidifier equipment cost of 50 million), annual operating costs to save more than 13 million yuan.

Biomedical clean room and its air-conditioning system
Bio-pharmaceutical industry workshop on cleanliness requirements, high requirements for constant temperature and humidity, generally control 18-26 ℃, 45-65% RH, the actual operation process, often appear overcooling and reheating the scene, in order to control the humidity to drop the temperature is very low, in order to the temperature and then heated, resulting in a waste of energy consumption. Denis environment after years of design experience, developed for the cold load is small, humidity and the requirements of energy-saving system solutions, and applied for a patent.
Eg. A biopharmaceutical plant, found that the air conditioning operation of high electricity costs, contact Denis environment, we applied the company's patented energy-saving system solutions, invested less than 200,000 yuan in renovation costs, annual energy-saving costs of 1.2 million yuan, a great improvement in the customer air-conditioning energy consumption of high issues.
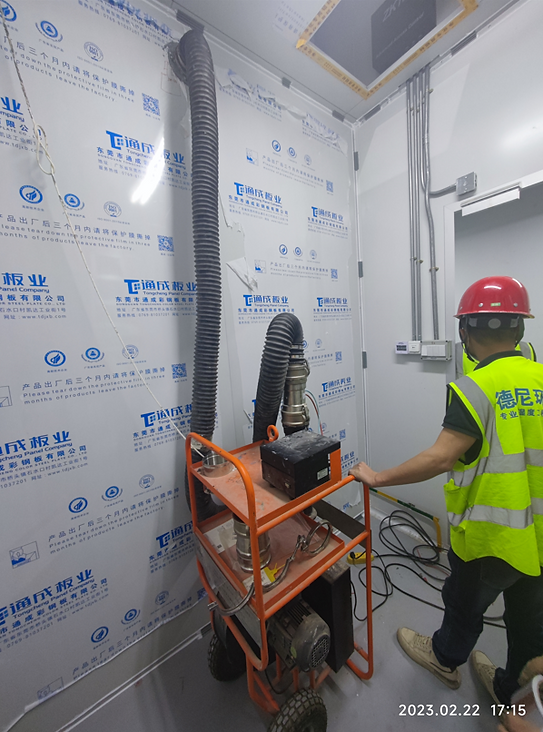
Drying Room Enclosure & Duct Construction Technology
Drying Room Enclosure Sealing
The sealing of the drying room enclosure plays a critical role in maintaining the low-humidity environment necessary for high-precision production processes, such as lithium battery manufacturing. A well-sealed enclosure ensures that moisture from external sources does not infiltrate the controlled environment, while also optimizing energy efficiency. Effective sealing involves high-tightness construction materials and techniques to minimize the risk of leakage and maintain consistent humidity levels.
Patented Technology for High-Tightness Lithium Drying Room
Our patented technology for lithium drying rooms ensures that the internal environment is maintained at extremely low humidity levels, often requiring conditions as low as 0.1% RH. This technology is specifically designed for the unique challenges of lithium battery production, where the drying process must be conducted in an ultra-dry environment to prevent moisture-related damage to components. With innovations in sealing methods, this patented system guarantees higher efficiency and lower operational costs compared to traditional systems.
Patented Air Shower Room Technology
An air shower room, commonly used in environments like cleanrooms and drying rooms, is designed to remove contaminants from personnel and equipment before they enter critical areas. Our patented technology for air shower rooms integrates high-efficiency filtration systems, powerful airflow dynamics, and optimized chamber designs to ensure personnel and materials are thoroughly decontaminated. This system prevents contamination from entering the controlled environment, ensuring the integrity of the production process.
Proprietary Color Steel Plate Splicing Sealing and Gluing Process
A key component of our sealing technology is the proprietary splicing and gluing process for color steel plates used in the construction of drying room enclosures. This process ensures seamless, airtight connections between steel plates, preventing leaks and maintaining the controlled internal environment. By utilizing advanced weather-resistant sealants, the structure maintains its integrity even under harsh conditions, providing long-term performance and durability.
Adoption of Weather-Resistant Sealant
The use of high-quality, weather-resistant sealants is crucial in maintaining the airtightness of drying room enclosures. These sealants are specifically formulated to withstand environmental fluctuations, preventing degradation over time. This ensures that the enclosure maintains its high-tightness properties, reducing the risk of humidity infiltration, energy loss, and system inefficiencies.
Proprietary Purification Door and Transfer Window Sealing Structure
Our proprietary purification doors and transfer windows are engineered with advanced sealing structures to ensure zero leakage when materials or personnel are transferred into or out of the drying room. These doors and windows are vital for maintaining the integrity of the cleanroom environment, preventing contamination and moisture ingress.
Combined Envelope Leakage Rate
The combined envelope leakage rate of a drying room enclosure is a critical indicator of the overall effectiveness of its sealing system. Our advanced sealing technology achieves a leakage rate of less than 1.2%, significantly outperforming traditional construction methods, which typically have a leakage rate of 5.0%. This improvement of 3.8 percentage points demonstrates the superior performance of our proprietary sealing techniques, ensuring a more stable environment and reduced energy consumption.
Case Study: Lithium Battery Production Workshop
Example of Drying Room Enclosure Engineering
A lithium battery production workshop designed for specific environmental conditions, such as -60°C dew point and 22±4°C ambient temperature with a cleanliness level of 100,000 class, requires precise control of temperature, humidity, and particulate contamination. In this environment, the sealing of the drying room is essential for maintaining stable conditions. The drying room enclosure uses cutting-edge sealing technology to ensure minimal leakage, allowing for a more energy-efficient and cost-effective operation.
Real-Time Data and Performance Metrics
In the real-world implementation of our technology, we have collected valuable performance data from a lithium battery production workshop. The following data points illustrate the efficiency of our system:
-
Air Volume (CMH): The system maintains optimal airflow to ensure the drying room environment is properly ventilated without introducing unwanted moisture.
-
Test Pressure (Pa): Pressure measurements are continuously monitored to ensure stability within the drying room, preventing leaks and moisture intrusion.
-
Leakage Rate (%): With our advanced sealing system, the leakage rate remains under 1.2%, significantly lower than the traditional rate of 5.0%.
Lithium battery production requires a nearly continuous low-humidity environment, with humidity levels typically maintained below 1% RH and sometimes as low as 0.1% RH. The production areas are large, with few personnel, making conventional designs lead to high initial investments in dehumidification equipment and significant air-conditioning operating costs. Through years of experience, our company has developed a patented system solution for precise control of temperature, humidity, and cleanliness, optimizing both energy efficiency and system performance.
For example, a lithium-ion plant used a traditional design for dehumidification, leading to excessive initial investment in dehumidification equipment and high operating costs. Our company proposed an energy-saving patented solution, which saved the client an estimated 10 million yuan in initial investment costs (50 million yuan for dehumidifier equipment). Furthermore, the annual operating costs were reduced by more than 13 million yuan, demonstrating significant cost savings without compromising environmental performance.
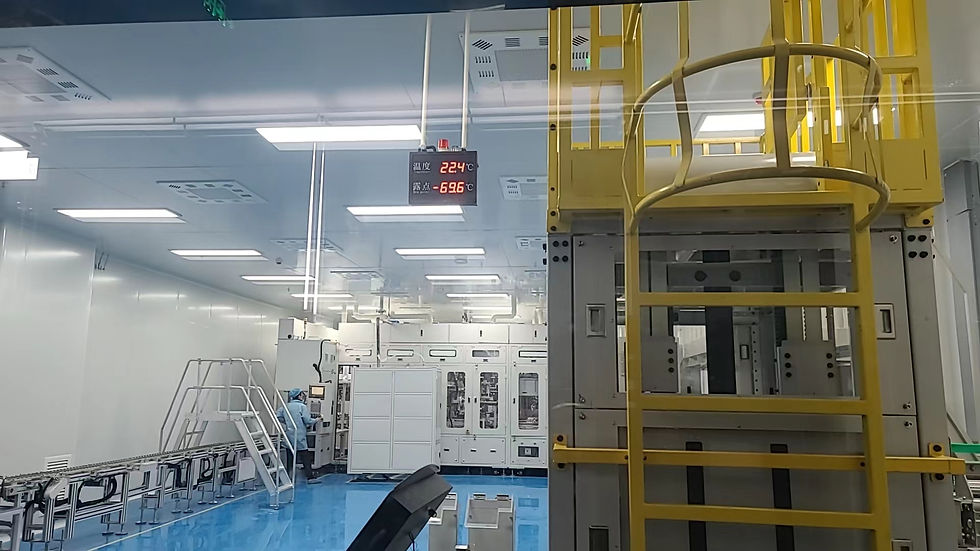
Low Humidity / Constant Temperature / Ultra Clean Total Solution
Denis design and project management teams are experienced in designing optimal and reasonable solutions for low humidity, constant temperature and ultra-clean environ- ments, including system design and selection, construction and technical process man- agement, as well as operation and maintenance.For example: In the manufacturing process of lithium-ion batteries, the impact of environ- mental humidity on the safety of lithiumion products and the consistency of product elec- trochemical performance is critical. From the paddle to the liquid injection process, the lithiumion battery production environment must be strictly controlled.High standards of environmental production require strict control of humidity, temperature and cleanliness to ensure product quality qualification rate and consistency.
-
Ultra-low dew point rotor dehumidification unit design, can realize the ambient dew point temperature as low as -50 ~ -80 ℃.
-
Low-humidity workshop adopts high-tightness construction design toensure that the air leakage rate of the wind system is no more than 0.5% and that there is no leakage in the drying room
-
For environments with high cleanliness requirements, particles can be controlled down to Class 10 cleanliness.
-
For the constant temperature requirements of high process environment workshop, the constant temperature accuracy can reach ± 0.3 ℃